Aluminum is an absolute staple in any machine shop. It is one of the most machinable metals out there, so it can be machined quickly and efficiently. That’s why it’s tough. Machining aluminum is a really competitive field since everyone is cutting it. This is especially true for production processing. In this article, I’ll share everything you need to know so you can properly manufacture your Aluminum Machining Parts like a pro.
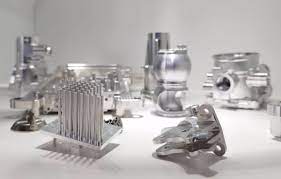
Why Is the Machining of Aluminum Machining Parts Challenging?
Aluminum is the most affordable and popular metal. However, due to the various methods of processing workpieces made of this material, high-quality Aluminum Machining Parts can only be obtained by selecting the correct aluminum model for processing.
Because this metal is soft, it has a low melting temperature. If you are a little careless, you may not only not get the processed parts that satisfy you but also waste aluminum.
When making Aluminum Machining Parts, you can have difficulty cutting aluminum, especially the sheet metal layers. It is related to frictional heat, which often exceeds the melting point of aluminum.
In addition, the metal has low hardness, and using rough cutting tools may wrinkle or stretch the entire workpiece.
Types of Aluminum Machining Parts
There are numerous usual types of aluminum parts of manufacture. Additionally, seven grades of lightweight aluminum alloys can be distinguished.
1. 2024-T351 Aluminum. It is the hardest aluminum and also is primarily made use of in airplanes. It is also recognized for being hard to machine, as it requires specialized tools and also certain making setups.
2. Lightweight aluminum alloy aluminum foil. In contrast, it is the most versatile aluminum and can be machined with a restricted variety of machining choices.
3. Aluminum plate. It is the type in which aluminum work surfaces are manufactured. Sheet steel layers can be obtained by hammering, marking, or rotating. While doing so, different kinds of lightweight aluminum can be incorporated for extra buildings.
4. Compound lightweight aluminum. You may have heard it dealt with aluminum. It has any kind type of coating such as zinc, silicon, nickel, or magnesium. The treated lightweight aluminum is durable and also has additional efficiency thanks to the finishing.
5. Pure/bare aluminum. As the name suggests, it is a pure, unworked metal. Generally, it needs to be made use of better in the production process.
It is rarely used as a product for work surface prep work as well as various other component manufacturing. This is due to an absence of deterioration resistance and also reduced sturdiness.
6. Lightweight aluminum alloy. Lastly, there are 8 grades (collection) of aluminum. Each of them has different residential or commercial properties and also a unique field of application.
The 1000 collection is 99% lightweight aluminum.
The 2000 series is aluminum alloy plus copper.
The 3000 collections are aluminum alloys containing manganese.
The 4000 collections are lightweight aluminum alloys containing silicon.
The 5000 series is a magnesium-aluminum alloy. >
The 6000 series are aluminum alloys consisting of magnesium and silicon.
The 7000 collection is an aluminum alloy strip.
Cutting Tools for Aluminum Machining Parts
Under no circumstances should you use a general-purpose knife to cut aluminum. Technically it will work, but aluminum is nothing like steel. Here are a few aspects of tool selection that will help you get the most out of your machine.
Cutting Tool Material
Hopefully, that’s a no-brainer for you. Even in non-performance applications, carbide will exceed high-speed steel in value for both costs of the tool over service life and in surface finish.
Even still, there are a few good things to know about carbide that will help you match up the perfect tool for the job.
Essentially we just need to understand what we want out of a tool. Aluminum is soft cutting, meaning that the tool doesn’t undergo hard impact forces as it cuts.
What’s critical is maintaining a razor-sharp edge. For this reason, we would choose hardness over toughness for material characteristics.
There are two main things that affect this property: carbide grain size and binder ratio.
For grain size, larger grain produces a harder material, whereas smaller grain produces a more impact-resistant, tough material. For aluminum, we want to maintain that edge sharpness, so we want a small grain size for maximum edge retention.
The other factor is the binder ratio. For carbide-cutting tools, the binder is cobalt. This could have anywhere from 2%-20% cobalt content. Since cobalt is softer than the carbide grains, more cobalt means a tough tool, and less cobalt means a harder tool.
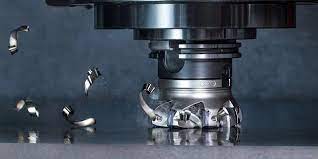
So we’re basically just looking for a carbide cutter that has a large grain size and low cobalt content.
Flutes
3 grooves are the pleasant place for strong carbide endmills 98% of the moment. Chip clearance is the name of the game for lightweight aluminum, and also 3 flutes give you the best balance of device toughness and chip clearance.
2 grooves can be a viable alternative where cutting forces are reduced and chip clearances are even more of an element. This can likewise be a means to reduce cutting pressures for light, doubtful cuts. One area where this makes good sense is when you have a very long tool that is prone to vibration. 2 grooves cut gently, so it may assist you to manage resonance.
At the end of the day, however, 3 flutes is the sector requirement. For bigger tools, like covering mills, this variety of flute’s wonderful spot will certainly vary by diameter. The secret right here is to have a big quantity of chip clearance so nothing gets plugged up. Nobody desires a constipated device at 700 IPM.
Helix Angle
Right here’s the equilibrium we’re attempting to strike: a smaller helix angle will decrease warmth because it’s reducing for much less time. A higher helix is smoother cutting and gives a wonderful surface area finish, however, creates much more heat.
If your device warms up, the aluminum will certainly weld itself on it, and also it’s game over. It occurs in much less than a 2nd; all you hear is the spindle load skyrocket and also break!
So here’s a strong general rule that’s benefited me for several years:
For roughing, a reduced helix angle of about 35 levels functions terrific. This keeps the device cool, and also no one appreciates surface area coating when roughing.
For finishing, a greater helix angle of 45 degrees is a total rock star. Certain it generates much more warmth, however, for light finishing cuts at high feed rates, that cares? The smooth reducing leaves a gorgeous and exact surface finish.
For something that will certainly do both roughing and ending up alright sufficient, select a 40-degree helix angle
Roughing: 35-level helix angle
Ending up: 45-degree helix angle
Multi-purpose: 40-level helix angle.
Worthwhile Features of Aluminum Machining Parts
Beyond those basics, there are a few other things that could give you that extra edge.
One thing that I’ve had great success with is polished tools. When the cutting flutes are polished smooth, the aluminum glides across them smoothly. Since there’s so little friction, the tool life goes through the roof and you can push them faster.
This is really worthwhile if you’re doing performance aluminum milling.
Another thing worth mentioning is tool coatings. In general, uncoated tools are the way to go. You won’t get much performance out of special coatings, and the more “standard” tool coatings will do more damage than good.