The construction industry is undergoing a paradigm shift, driven by the emergence of innovative materials that push the boundaries of design and sustainability. Among these rising stars, aluminum square tubes are carving a distinct niche with their unique blend of exceptional strength-to-weight ratio, corrosion resistance, and unparalleled formability. This article delves into the technical prowess of aluminum square tube structures, exploring their multifaceted applications and potential to transform the built environment.
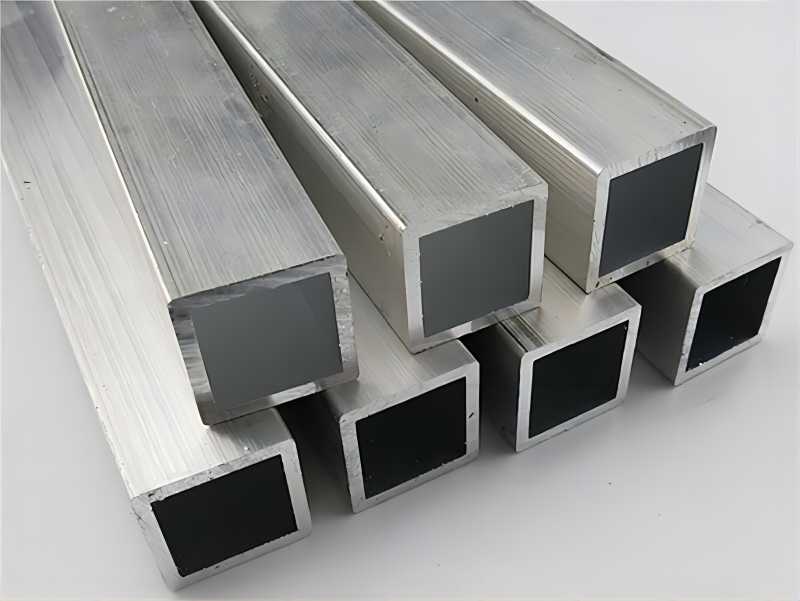
Material Properties of Aluminum Square Tubes
1. Strength-to-Weight Ratio
Aluminum square tubes exhibit a superior strength-to-weight ratio compared to traditional steel counterparts. This means they can maintain comparable or even higher load-bearing capacities while weighing significantly less. This translates into numerous advantages:
- Optimized Structural Design: Reduced material weight allows for lighter beams, trusses, and columns, minimizing foundation requirements and overall building mass.
- Enhanced Efficiency: The lighter weight facilitates faster construction timelines and reduces transportation costs associated with material delivery.
- Long-Span Capabilities: High specific strength enables aluminum square tubes to span greater distances effectively, ideal for large open spaces and architectural flexibility.
2. Corrosion Resistance:
One of aluminum’s key characteristics is its inherent corrosion resistance. The spontaneous formation of a protective oxide layer shields the metal from environmental degradation, particularly beneficial in:
- Harsh Environments: Coastal regions, industrial areas, and areas with high air pollution are where aluminum’s corrosion resistance truly shines, minimizing maintenance requirements and extending the lifespan of structures.
- Reduced Maintenance Costs: The natural passivation layer eliminates the need for frequent painting or additional protective coatings, leading to long-term cost savings.
- Aesthetic Integrity: Aluminum’s inherent resistance to corrosion preserves its surface finish and maintains the architectural integrity of the building.
3. Ductility and Formability:
Aluminum stands out for its outstanding ductility and formability, making it highly adaptable to diverse design requirements. This characteristic manifests in several ways:
- Complex Geometries: Architects and engineers can readily shape aluminum square tubes into intricate forms, enabling unique and expressive architectural features.
- Precise Fabrication: The material’s malleability allows for precise cutting, bending, and welding, ensuring adherence to stringent design specifications.
- Versatility in Applications: From intricate facade systems to custom-designed interior elements, aluminum’s formability facilitates diverse applications within the same structure.
4. Sustainability
In modern construction, environmental considerations are paramount. Aluminum square tubes excel in this regard due to their:
- High Recyclability: Aluminum boasts an impressive recycling rate, significantly reducing landfill waste and promoting resource conservation.
- Reduced Energy Consumption: The lightweight nature of aluminum structures minimizes the embodied energy associated with material production and transportation, lowering the overall environmental footprint.
- Durable & Low-Maintenance: The combination of corrosion resistance and minimal maintenance requirements translates to extended product lifecycles, further reducing resource consumption and environmental impact.
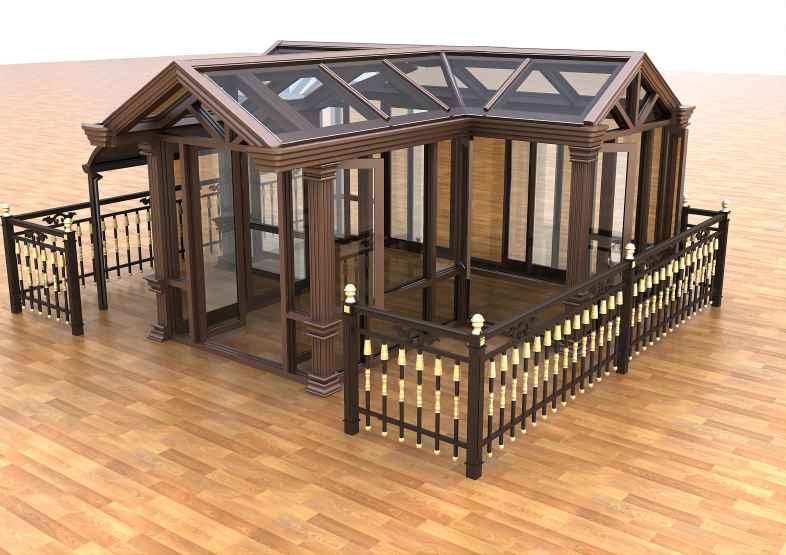
Structural Applications of Aluminum Square Tubes
1. Building Framing
Aluminum square tubes excel in building framing applications due to their:
- High Specific Strength: They can sustain significant loads while minimizing the overall weight of the framing system, enabling optimized foundation design and reduced material consumption.
- Dimensional Stability: Aluminum exhibits minimal thermal expansion and contraction, contributing to dimensional accuracy and improved structural integrity of the building.
- Ease of Assembly: Pre-fabricated and lightweight, aluminum square tubes facilitate faster and more efficient construction processes, leading to reduced on-site labor costs.
- Versatility: The availability of various sizes and wall thicknesses allows for the construction of diverse wall, floor, and roof framing systems, catering to varied structural requirements.
2. Long-span Trusses and Beams
The exceptional strength-to-weight ratio of aluminum square tubes makes them ideal candidates for long-span trusses and beams, enabling:
- Large Open Spaces: These structural elements can effectively bridge wider spans without additional support, allowing for unobstructed floor plans and expansive interior volumes.
- Reduced Structural Depth: Compared to traditional materials, aluminum beams and trusses require less depth for equivalent load-bearing capacities, maximizing usable space within the building.
- Architectural Flexibility: Their formability allows for the creation of custom truss and beam configurations, accommodating unique design requirements and enhancing building aesthetics.
3. Curtain Wall and Cladding Systems
Aluminum square tubes are a favored choice for curtain wall and cladding systems due to their:
- Lightweight Construction: They minimize the dead load on the building structure, contributing to overall stability and efficient foundation design.
- Aesthetics and Flexibility: The smooth, clean lines and ability to accommodate various finishes offer architects and designers exceptional aesthetic freedom for creating modern and elegant building envelopes.
- Weather Resistance: The inherent corrosion resistance of aluminum protects against environmental degradation, ensuring long-term durability and minimal maintenance requirements for facade systems.
- Modular Installation: Pre-assembled panels and profiles enable efficient onsite installation, reducing construction time and costs.
4. Diverse Interior Elements
Beyond structural applications, aluminum square tubes find extensive use in interior elements due to their:
- Strength and Stability: They provide robust support for columns, railings, and other load-bearing elements while maintaining a sleek and modern appearance.
- Fire Resistance: Specific aluminum alloys offer excellent fire resistance properties, making them suitable for applications requiring enhanced safety considerations.
- Formability and Design Versatility: Aluminum’s ductility allows for the creation of custom interior elements, such as decorative screens, partitions, and furniture features, contributing to unique and personalized spaces.
- Corrosion Resistance and Low Maintenance: The inherent passivation layer ensures minimal maintenance is required for interior elements, reducing long-term operational costs.
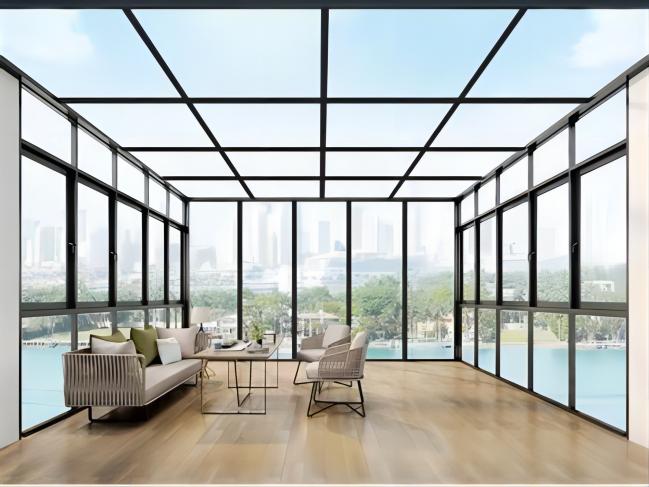
Advantages of Utilizing Aluminum Square Tubes in Building Structures
1. Optimized Structural Design and Reduced Costs
- Minimized Foundation Requirements: The significantly lower weight of aluminum square tube structures compared to traditional steel counterparts translates to reduced foundation loads and smaller foundation sizes. This translates to significant cost savings in foundation design and construction.
- Reduced Transportation and Handling Costs: The lighter weight also translates to lower transportation costs, both in terms of fuel consumption and vehicle requirements. Additionally, the ease of handling and pre-fabrication of aluminum components further minimizes labor costs associated with onsite construction.
2. Enhanced Construction Efficiency and Speed
- Prefabrication and Modularization: Aluminum square tubes are readily available in pre-fabricated and modular forms, including beams, columns, and wall panels, allowing for rapid onsite assembly and significantly faster construction timelines compared to traditional materials requiring on-site fabrication and welding.
- Improved Workability and Installation: The inherent ductility and ease of cutting, drilling, and welding of aluminum square tubes facilitate efficient installation processes, further contributing to faster construction times and reduced labor requirements.
3. Improved Building Energy Performance
- Reduced Thermal Mass: The significantly lower thermal mass of aluminum structures compared to steel or concrete translates to faster thermal response, enabling efficient heating and cooling systems to react quickly to changing temperature conditions. This leads to lower energy consumption for both heating and cooling throughout the building’s lifespan.
- Enhanced Envelope Performance: The lightweight nature of aluminum allows for the design of high-performance building envelopes, incorporating advanced insulation and cladding systems that further optimize thermal efficiency and minimize energy losses.
4. Architectural Design Flexibility and Freedom
- Formability and Versatility: The inherent ductility of aluminum allows for the creation of complex shapes and intricate geometries, enabling architects and designers to express their creativity and design unique and innovative building forms that are difficult or impossible to achieve with traditional materials.
- Wide Variety of Finishes and Aesthetics: Aluminum readily accepts various surface treatments and finishes, including anodizing, painting, and powder coating, offering extensive design flexibility and the ability to create visually striking and aesthetically pleasing buildings.
5. Long-Term Durability and Low Maintenance
- Natural Corrosion Resistance: Aluminum’s inherent oxide layer provides excellent protection against corrosion, significantly reducing the need for maintenance and protective coatings, especially in harsh environments. This translates to lower lifetime maintenance costs and increased structural integrity over time.
- High Strength-to-Weight Ratio: The exceptional strength-to-weight ratio of aluminum ensures the structural integrity and stability of buildings, even in lightweight configurations, contributing to long-lasting performance and reduced risk of structural failure.
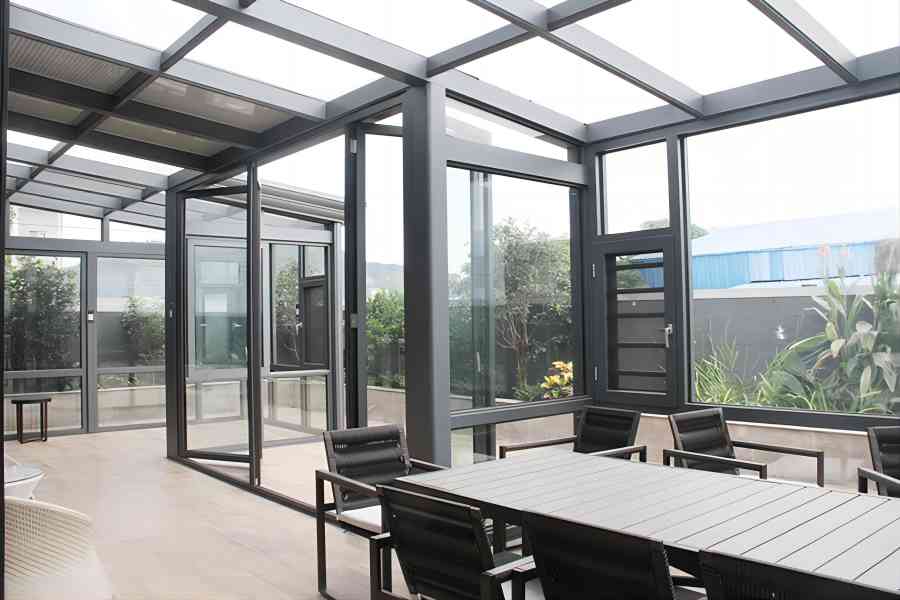
Considerations for Utilizing Aluminum Square Tubes in Building Structures
1. Initial Cost vs. Life-Cycle Cost Analysis
While the initial cost per unit weight of aluminum may be higher than some traditional materials like steel, it is crucial to consider a comprehensive life-cycle cost analysis. The significant cost savings achieved through reduced weight, faster construction, and lower maintenance throughout the building’s lifespan can often offset the initial investment. Factors such as:
- Foundation cost reduction: The lighter weight of aluminum structures can lead to smaller and less expensive foundation requirements.
- Reduced transportation and handling costs: The lower weight translates to lower fuel consumption and handling costs during material transportation.
- Faster construction timelines: Prefabrication and ease of assembly can significantly reduce construction time and labor costs.
- Lower maintenance costs: Aluminum’s natural corrosion resistance minimizes the need for maintenance and repainting, leading to long-term cost savings.
Therefore, a comprehensive analysis considering both initial and ongoing costs is essential to accurately evaluate the economic viability of using aluminum square tubes in a specific project.
2. Thermal Expansion and Contraction Management
Aluminum has a higher coefficient of thermal expansion than steel, meaning it expands and contracts more with temperature changes. This needs to be carefully factored into the design of aluminum structures to prevent:
- Differential movement: Uneven expansion or contraction between aluminum and other materials can lead to stress concentrations and structural problems.
- Joint failures: Proper design and selection of expansion joints and other movement accommodation strategies are crucial to ensure the integrity of connections and prevent sealant failure.
- Acoustic issues: Thermal expansion and contraction can generate noise in buildings, which needs to be addressed through appropriate design measures and material selection.
By implementing appropriate engineering solutions and construction practices, the challenges associated with thermal expansion and contraction can be effectively managed, ensuring the long-term performance and structural integrity of aluminum buildings.
3. Fire Resistance and Code Compliance
While certain aluminum alloys offer good fire resistance properties, some applications may require additional fireproofing measures to comply with building codes and safety regulations. Factors to consider include:
- Building occupancy and fire risk: High-risk occupancies or buildings with large occupant loads may require additional fire protection for structural elements.
- Specific fire resistance requirements: Building codes often specify minimum fire resistance ratings for structural components, which may necessitate additional measures for aluminum elements.
- Fireproofing options: Various fireproofing materials and methods are available for aluminum structures, such as intumescent coatings, cementitious sprays, and mineral wool insulation.
Selecting the appropriate aluminum alloy and fireproofing strategy based on the specific project requirements and local building codes is crucial to ensure fire safety and compliance.
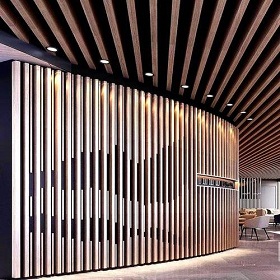
Conclusion
Aluminum square tube structures offer a compelling alternative to traditional building materials. Their unique combination of strength, lightweight nature, versatility, and sustainability makes them a valuable choice for architects, engineers, and builders seeking innovative and efficient construction solutions.