Aluminum has been a key player in the aviation industry for decades, primarily due to its exceptional strength-to-weight ratio, corrosion resistance, and overall versatility. Within the realm of aircraft construction, one of the most critical components is the aluminum tube. These tubes serve a wide range of functions, from structural elements to hydraulic systems. In this article, we will delve into the properties, applications, and manufacturing processes of aircraft aluminum tubes, shedding light on their significance in modern aviation.
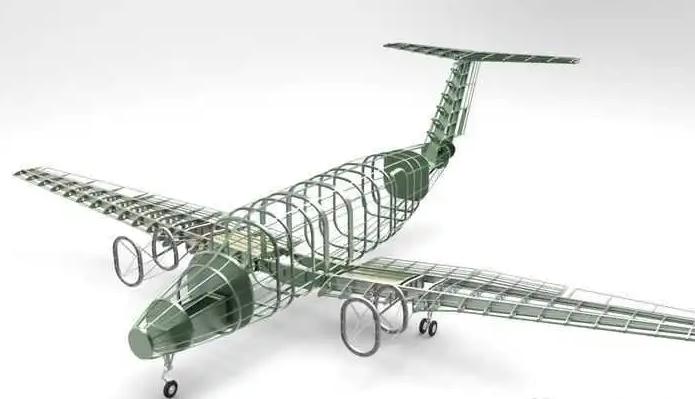
Properties of Aircraft Aluminum Tubes
Aircraft aluminum tubes are engineered to meet stringent performance requirements, making them stand out among materials used in the aerospace sector. Some of the notable properties of these tubes include:
- Lightweight: Aluminum’s low density makes it an ideal choice for reducing overall aircraft weight. This is crucial in enhancing fuel efficiency and overall performance.
- High Strength: Despite its lightweight nature, aluminum is remarkably strong, allowing aircraft aluminum tubes to withstand high stresses and loads. This characteristic is essential for structural components.
- Corrosion Resistance: Aluminum naturally forms a protective oxide layer, making it highly resistant to corrosion, even in the harsh conditions of the aerospace environment.
- Malleability and Ductility: Aluminum can be easily shaped and formed into various tube profiles without compromising its structural integrity, thanks to its malleability and ductility.
- Thermal Conductivity: Aircraft aluminum tubes have excellent thermal conductivity properties, which help dissipate heat generated by various systems on an aircraft.
- Non-Magnetic: Aluminum is non-magnetic, which is crucial for aircraft where magnetic interference can be a concern.
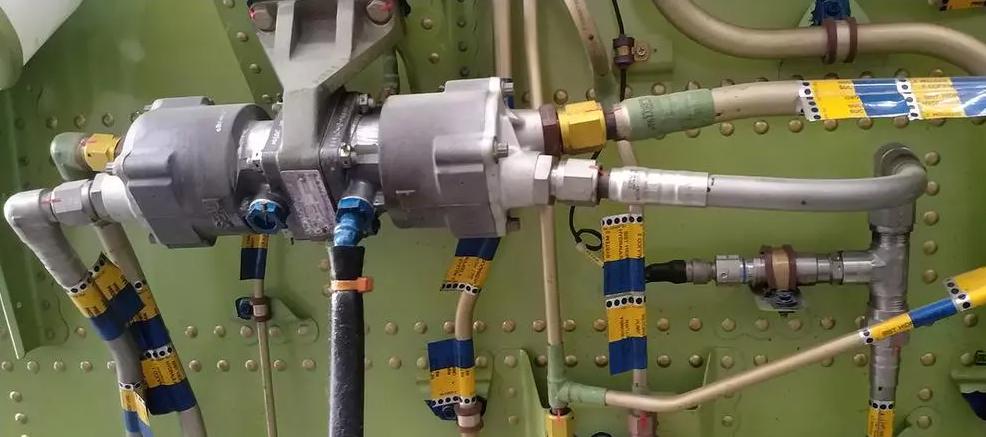
Applications of Aircraft Aluminum Tubes
Aircraft aluminum tubes find numerous applications in different areas of aviation. Some of the key uses include:
- Structural Components: They are used in the construction of the aircraft’s frame and fuselage, providing stability and support.
- Hydraulic Systems: Aluminum tubes are employed in hydraulic systems to transport fluids and ensure the smooth operation of landing gear, brakes, and other critical components.
- Cooling Systems: Aluminum tubes are used in the heat exchangers and cooling systems of an aircraft to maintain optimal operating temperatures.
- Fuel Systems: They play a pivotal role in fuel distribution and storage systems, ensuring the safe and efficient transportation of aviation fuel.
- Instrumentation: Aluminum tubes are integral to various instrumentation and control systems within the aircraft.
- Pneumatic Systems: These tubes are crucial for pneumatic systems used for cabin pressurization, air conditioning, and more.
- Exhaust Systems: Aluminum tubes are utilized in the exhaust systems, helping to transport hot gases away from the engine.
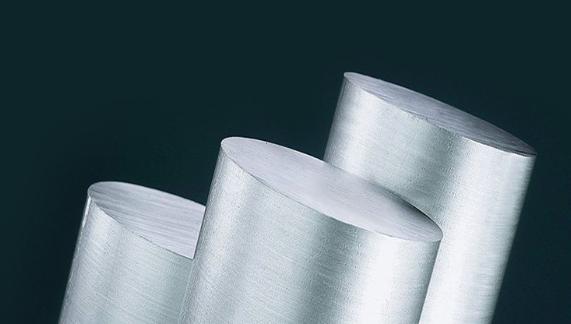
How to Manufacturing Aircraft Aluminum Tubes?
The manufacturing of aircraft aluminum tubes involves a series of precision processes to ensure they meet the demanding requirements of the aerospace industry. Some of the key steps in the manufacturing process include:
- Billet casting: The first step is to cast the aluminum alloy into billets, which are solid cylindrical or rectangular blocks of metal. The billets are cast in a variety of sizes and shapes, depending on the desired final dimensions of the tube.
- Extrusion: The billets are then extruded through a die to form the Aircraft Aluminum Tube shape. The extrusion process involves forcing the billet through a tapered opening, which reduces the cross-section and increases the length of the tube.
- Drawing: The extruded Aircraft Aluminum Tube is then drawn through a series of dies to reduce its diameter and wall thickness. The drawing process also helps to improve the surface finish and dimensional accuracy of the tube.
- Annealing: The drawn Aircraft Aluminum Tube is then annealed, which is a heat treatment process that softens the metal and improves its ductility. Annealing is necessary to prepare the tube for the next step in the manufacturing process.
- Sizing: The annealed Aircraft Aluminum Tube is then sized to ensure that it meets the required dimensional tolerances. This is done by passing the tube through a series of rollers that apply pressure to the outside of the tube.
- Cutting: The sized Aircraft Aluminum Tube is then cut to the desired length. This is typically done using a saw or a waterjet cutter.
- End finishing: The ends of the Aircraft Aluminum Tube are then finished to prepare them for welding or other joining operations. This may involve machining the ends of the tube to a specific diameter or shape or chamfering the ends to reduce the risk of cracking.
- Inspection and testing: The finished Aircraft Aluminum Tube is then inspected and tested to ensure that it meets all of the required quality standards. This may involve visual inspection, dimensional inspection, and non-destructive testing methods such as radiography or ultrasonic testing.
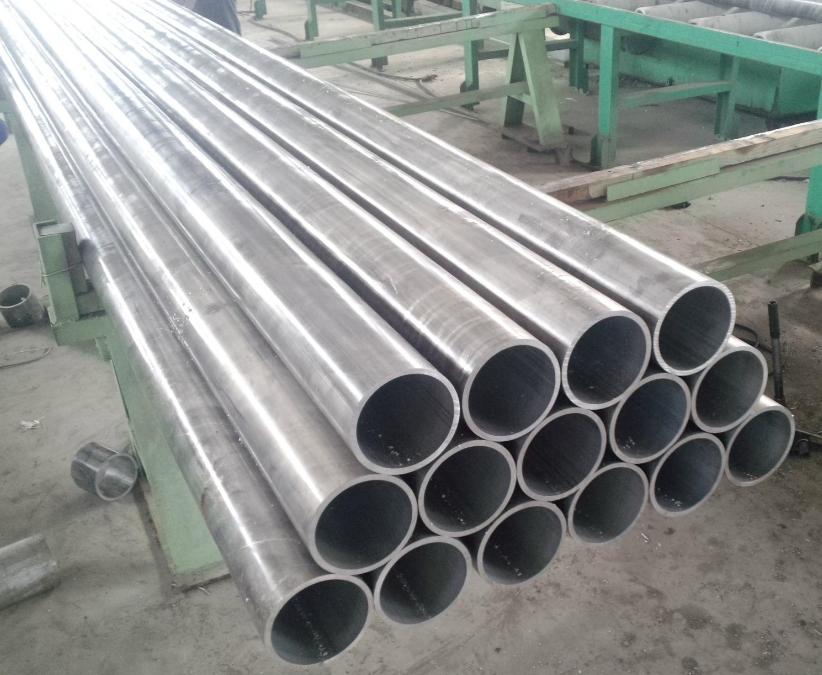
Conclusion
In conclusion, aircraft aluminum tubes are fundamental components that underpin the structural integrity and functionality of modern aircraft. Their exceptional properties, such as lightweight strength and corrosion resistance, have made them indispensable in various aviation applications. The meticulous manufacturing processes employed in their production ensure that these tubes meet the stringent safety and performance standards of the aerospace industry, ultimately contributing to safer and more efficient flight. As technology continues to advance, we can expect further innovations in the production and application of aircraft aluminum tubes, further improving the future of aviation.